ステンレスは、耐食性、強度、美観に優れ、医療機器や食品機械など、サニタリー性と意匠性が求められる分野で使用されています。ステンレス製の部品加工において、品質を大きく左右する工程が溶接になります。
ステンレス(SUS)の溶接と特長
ステンレス鋼は、鉄を主成分にクロムを10.5%以上含む合金鋼です。クロムが酸素と結合することで表面に不動態皮膜と呼ばれる薄い膜を形成しています。ステンレス鋼は、大きく分けて「オーステナイト系」「フェライト系」「マルテンサイト系」の3種類に分類されます。
最も使用されているのはオーステナイト系で、耐食性、溶接性、加工性に優れており、様々な用途に用いられています。フェライト系はオーステナイト系よりも耐食性はやや劣りますが、磁性を持つという特徴があります。マルテンサイト系は熱処理によって硬化させることができ、強度と耐摩耗性に優れています。
高い耐食性を持つステンレス鋼を溶接する場合、溶接部も母材と同等の耐食性を維持することが求められます。また、前述した通り意匠性の高い製品に使用されるため、溶接不良の回避が必要になります。しかし、 熱伝導率の低さや加工硬化、溶接部の耐食性確保という点から溶接難易度は高く、高い溶接技術が必要になります。
ステンレス(SUS)を溶接する際の溶接工法
ステンレス溶接に使用される工法として、メインとなるのでTIG溶接、MIG溶接、レーザ溶接です。それぞれ、メリット・デメリットがあり、高品質な溶接を行うためには、適切な工法を選択する必要があります。
TIG溶接
TIG溶接は、タングステン電極を用いてアークを発生させ、溶加材を添加しながら溶接する工法です。不活性ガスであるアルゴンガスをシールドガスとして使用することで、溶接部を大気から保護し、酸化を防ぎます。TIG溶接は、高い精度で溶接が可能で、美しい仕上がりを得られることが特徴です。薄板から厚板まで幅広く対応できます。溶接部の品質が高く、スパッタが少ないというメリットがある一方、溶接速度が遅く、熟練した技術が必要というデメリットもあります。
MIG溶接
MIG溶接は、ワイヤを電極としてアークを発生させ、自動的に溶接する工法です。TIG溶接と同様に、アルゴンガスなどの不活性ガスをシールドガスとして使用します。MIG溶接は、溶接速度が速く、厚板の溶接に適していることが特徴です。作業効率が高く、深い溶け込みが得られるというメリットがある一方、TIG溶接に比べて精度が低く、スパッタが多いというデメリットもあります。
レーザ溶接
レーザ溶接は、レーザ光を熱源として溶接する工法です。集光された高エネルギーのレーザ光によって、材料を溶融・接合します。レーザ溶接は、高速溶接が可能で、熱影響部が狭く、精密な溶接が可能なことが特徴です。変形が少なく、高い品質の溶接が可能というメリットがある一方、設備コストが高く、適用材料が限られるというデメリットもあります。
ステンレス(SUS)を溶接する際の注意点
ステンレスを溶接する際には、材料の種類によって注意すべき点が異なります。大きく分けて、オーステナイト系、フェライト系、マルテンサイト系の3種類があり、それぞれ特有の性質を持っているため、溶接の難易度も変わってきます。
オーステナイト系ステンレス鋼の溶接
最も一般的なステンレス鋼ですが、溶接においては高温割れ、鋭敏化、熱歪みと残留応力に注意が必要です。
高温割れは、リンや硫黄などの不純物元素が原因で発生します。溶接金属中に適切な量のδフェライトを含有させることで、高温割れを防止できます。δフェライトは、これらの不純物元素を固溶しやすく、割れを抑制する効果があります。
鋭敏化は、500~800℃に加熱することで、炭素がクロムと結合し、粒界に炭化物を析出させる現象です。これにより、耐食性が低下する可能性があります。鋭敏化を防止するためには、溶接入熱を低く抑え、母材の炭素量を少なくすることが有効です。
熱歪みと残留応力は、ステンレス鋼の熱伝導率が低く、線膨張係数が高いため、発生しやすい問題です。溶接条件や継手形状を工夫することで、熱歪みを抑制し、残留応力を低減することが重要です。
フェライト系ステンレス鋼の溶接
高温で粒界が粗大化しやすく、延性や靭性が低下する傾向があります。そのため、溶接時は熱影響部を最小限に抑え、高温にさらされる時間を短縮することが重要です。また、350~550℃または600~800℃の温度域に長時間さらされると脆化が発生するため、注意が必要です。ただし、一度脆化が発生しても、再加熱と急冷によって脆化を解消できる場合があります。
マルテンサイト系ステンレス鋼の溶接
急激な冷却によって硬化する性質があるため、溶接熱影響部で割れが発生しやすくなります。これを防ぐためには、溶接部を清潔に保ち、溶接材料の乾燥を徹底することが重要です。また、予熱や後熱を行い、溶接部の拘束を少なくすることで、割れのリスクを軽減できます。高張力鋼の溶接方法を参考にすると良いでしょう。
これらの注意点に加えて、溶接前の準備、溶接中の操作、溶接後の処理など、基本的な溶接技術をしっかりと守ることが、高品質なステンレス溶接を実現する上で不可欠です。
ステンレス溶接後の仕上げと表面処理が必要な理由
ステンレスは耐食性に優れた金属ですが、溶接を施した後の仕上げや表面処理を適切に行わないと、酸化や錆が発生し、耐久性や美観を損なう恐れがあります。特に、溶接によって発生する酸化スケール(溶接ヤケ)や不均一な表面状態は、そのまま放置すると劣化を早める原因になります。
また、製品の用途によっては、高い外観品質が求められることも少なくありません。例えば、食品や医療機器などの分野では、衛生管理の観点からも滑らかで清潔な仕上げが必要になります。
ステンレスを接合する際に使用される工法
ステンレスは、その優れた耐久性と耐食性から、多岐にわたる産業分野で重宝されています。しかし、その特性を最大限に引き出すためには、用途に応じた適切な接合工法を選ぶことが不可欠です。ステンレスの接合には様々な方法が存在し、それぞれ独自の特徴と適用範囲を持っています。
当社のステンレス(SUSU)溶接事例
産業機械 一貫加工組立.comを運営する長谷金属のステンレス溶接事例を紹介します。
検査装置 ステンレス カバー 板金溶接
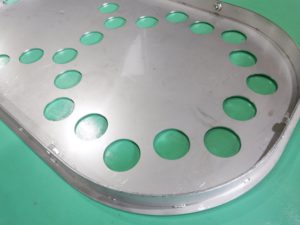
検査装置 ステンレス カバー 板金溶接
この検査装置 ステンレス製のカバーは、社内で一貫製作を行った 板金溶接 部品になります。このステンレス製のカバーはC1複合機のクリーンカットで抜き加工を行っています。クリーンカットではレーザー切断時に金属が酸化反応を起こした時に切断面、金属の表面に成形される酸化物の被膜を酸化被膜といい、切断時の不純物や焼けを巻き込んで被膜を成形する為、製品の表面処理によっては後に剥離などの問題が起こります。この切断表面を酸化させない為に、レーザー切断時のアシストガスに窒素ガスを使用してクリーンカット加工を選定しています。
検査機 ステンレス カバー 板金組立
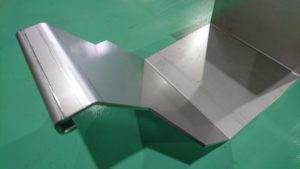
検査機 ステンレス カバー 板金組立
この 検査機で使用されるステンレス製カバーは社内で一貫加工製作された 板金組立部品です。検査機には駆動する為に油圧ユニットが組み込まれている事があり、油圧ユニット部からのオイルの飛び散りを外部に出さない様にする為に検査機の側面に組み込まれるカバーになります。これは外部からの埃や小さなゴミの侵入を防ぐ役割もある為、使用される材料はオイル・水に強いSUS材を使用しています。SUS材の特徴の部品が錆びにくく耐食性が良い事、熱にも強く耐熱性が良い事、劣化しにくく耐酸化性が高い事から部品を清潔に保て清掃・メンテナンス性の向上、長い期間部品を使用出来、劣化・腐食による部品交換が減らせコストダウンを実現出来ます。
検査機 ステンレス ボス付きブラケット 制御装置
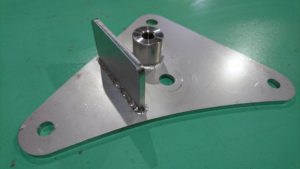
検査機 ステンレス ボス付きブラケット 制御装置
この 検査機 に使用されるステンレス製 の ボス付きブラケットは社内で一貫加工製作された 機械組立 部品です。検査機にもSUS材を使用した部品が多くあります。機械組立に使用される部品に必要とされる、ステンレスの特徴の部品が錆びにくく耐食性が良い事、熱にも強く耐熱性が良い事、劣化しにくく耐酸化性が高い事から部品を清潔に保て清掃・メンテナンス性が良いSUS材を使用した機械組立部品が増えています。
検査機 ステンレス オイルパン 水平型
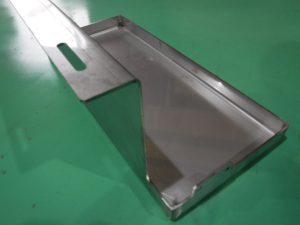
検査機 ステンレス オイルパン 水平型
この検査機 ステンレス製オイルパン水平型は、検査機に使用されている油圧シリンダの下部に取り付くオイルパンになります。オイルパンとは油を受けるための容器、受け皿のことで油の流出防止に使います。加工の方はC1複合機で抜き加工を行い、タップ加工後、曲げ加工を行います。次に溶接工程のTIG溶接で部材同士を強固に溶接を行っています。この時注意する事は、部材同士を合わせた時の隙間が無い様に溶接手順を決め加工を行い、オイルパン本体は油が漏れないように溶接箇所はすべて全周溶接を行います。溶接後は歪と専用の焼け取り機で溶接焼けを除去し仕上げています。
当社が提供するステンレス(SUS)溶接サービス
産業機械一貫加工組立.comを運営する長谷金属では、ステンレス溶接に関する強みを持ち、食品機械メーカー、環境装置メーカーの皆様に選ばれています。t1mm~8mmまでのステンレス板金溶接はもちろん、角パイプ・丸パイプ溶接にも対応し、お客様の多様なニーズにお応えします。TIG溶接、ファイバーレーザ溶接など、最適な溶接方法で高品質なステンレス溶接を実現します。製缶加工を得意としてきた当社では、大型製品のSUS溶接も可能で、L3000mmのSUS溶接の実績も保有します。
熟練の溶接工13名(2024年12月時点)が在籍し、長年の経験で培った技術と設備力で、高精度・高強度な溶接品を提供します。
当社に頂く、ステンレス(SUS)溶接に関するよくある質問
当社に頂く、ステンレス溶接に関するよくある質問を紹介します。
>>ステンレスで板厚は1.5mmのカバーの製作をお願いします。表面に傷などは厳禁で、溶接もありますが、加工可能ですか。
>>ステンレスの架台製作をお願いします。L230×W800×H450のサイズで、表面と底面に平行度0.1mmの公差があります。1台で良いのですが、5日程で製作可能でしょうか。
>>大型製缶加工について、SUSの対応は可能ですか?製缶板金から溶接、機械加工、表面処理まで検討しています。