① 材料の調達とトレーサビリティの確保
② 図面をもとにCAD・CAMデータ製作
③ ワークの形状製作
③ー1 ワークが丸物形状の場合
③ー2 ワークが角物形状の場合
④ 追加工工程
④ー1 穴加工・溝加工
④ー2 自由局面形状や端面の角部への精度だしなどの加工
④ー3 研磨加工仕上げ
⑤ 溶接工程
⑥ 組立工程
⑦ 表面処理工程
⑧ 検査納品
概要
日本国内には、金属加工業が数千社以上あり(従業員数10名以下もいれると、数万社以上存在)、その多くの金属加工業は、特定分野に特化した加工技術を得意としています。機械加工業における専門特化とは、微細な切削加工を得意としている企業が、ミクロン単位の加工が可能な工作機械と微細加工のための刃物を保有し、加工を行っている状況をさ日ます。同様に、丸い形状(円柱形状など)を専門特化で加工している機械加工業は、旋盤・自動盤・ターニング加工機などの工作機械とチップやバイトを保有しています。
機械加工は、製造業の代表的な加工であり、日本は大手メーカーを中心とした産業クラスターが形成されています。その結果、完成品メーカーの各パーツは内製化をされていることは非常に少ないと言えます。これは、機械加工部品においては金属や樹脂を切削する技術を持つ機械加工企業が担当し、鋼板を曲げる塑性加工は当該技術を得意としている板金加工業の企業が担当をしています。このように、各金属加工業が加工分野をそれぞれ担当して、自動車や工作機械や半導体製造装置など、高精度・高機能の製品を完成させることで、日本の製造業の産業クラスターは形成され、当社のような企業が日本の製造業における土台となっています。
この専門分野をそれぞれ持った金属加工業が存在していることは、日本のモノづくりの開発技術力、特に高精度の試作部品の製作には非常に向いています。しかし、発注する完成品メーカーは加工分野ごとに金属加工業を選定・選択する必要があり、また、それぞれの部品を組み立てる企業の手配もしくは、自社でのアッセンブリ(組立)が必要です。
発注する側からすれば、機械加工と組立(溶接や締結)を一貫加工してくれる金属加工業が協力サプライヤーとして存在していればよいのですが、日本の金属加工業の傾向は、特定分野の加工技術を専門としていることがほとんどです。その結果、高度な機械加工と溶接組立を行っている金属加工業の数は国内において、1000社もないといわれています。この要因としては諸説ありますが、特に機械加工においては工作機械の加工条件の設定や刃物選定(場合によっては刃物を自社製作している金属加工業も存在する)など、加工者のオペレーティング能力に対して求められる水準が高く、その結果、専門特化している企業が多いと言えます。
また、量産を得意としている機械加工業ほど、一人のオペレーターで複数の工作機械を担当し、いかに機械稼働をあげるかに重きを置くことが多くなっています。それに対して、溶接組立を得意としている金属加工業は、技術者の溶接技術や組立技術が1品ごとに必要になります。特に溶接と組立の工程があると、溶接によって発生した歪みの除去やそれを踏まえた組立技術が求められます。この技術にマニュアルはほぼ存在せず、技術職人の経験に依存していることがほとんどです。溶接技術にしても同じことが言え、腕の立つ溶接技術者とそうでない溶接技術者が実施した溶接痕を見れば、素人でもその違いがわかります。
つまり、組立溶接は、人の手・技術によるところが大きいことが特徴です。機械加工と溶接組立は、上記で述べたようなそれぞれの特徴によって、同じ金属加工業といえどもその技術特性の違いにより、全く異なる職業になります。その為、機械加工と溶接組立を一貫して加工をする金属加工業の社数は非常に少なくなるのです。ただ、ご発注者様からすると、機械加工と溶接組立を違う金属加工業に発注すると、製品・部品の手配工数や不良が出た際の原因究明・改善に工数がかかる要因となります。その為、各々1社で行う機械加工と溶接組立の工程を、内製化できる1社で行える金属加工業であれば、各工程の全体最適化によるコストダウンや、溶接や組立を加味した機械加工による加工工数の削減や、製品の保証等が容易になっています。このような理由から、昨今では『 機械加工 溶接組立 』が大手企業様を中心として求められています。
機械加工 溶接組立の工程
機械加工と溶接組立の工程の一例は以下の通りとなっています。『 産業機械 一貫加工組立.com 』を運用する長谷金属が実際に行っている加工工程を例にしてご紹介いたします。
① 材料の調達とトレーサビリティの確保
材料を調達し、加工・納品する上では、調達した材料の品質保証ができているかというのは、製品が実際に使われる場面において、安全性や信頼性の観点から非常に重要な要素となります。その観点で行くと、材料の品質を保証するミルシート(鋼材検査証明書)の確保は、製造業の企業にとって大切なことであると言えます。しかし、単品・小ロットの生産を取り扱うような企業にとっては、ミルシートを商社から直接入手することは困難であるとます。
一方で、産業機械 一貫加工組立.comでは、近隣のメーカー商社との長年の付き合いによりミルシート(鋼材証明書)の入手が可能となっており、お客様が求める安全性・トレーサビリティの確保が可能となっています。その為、機械加工だけを行う様な企業では特に難しいとされる、ブロック材や丸棒材などに対してもミルシート付きの材料調達が可能となります。
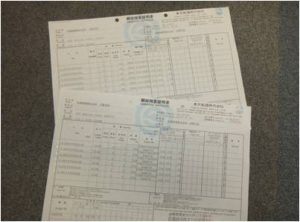
ミルシート
② 図面をもとにCAD・CAMデータ製作
製造業が加工を行う際には、メーカーから指定のある機械図面通りに加工を行うことが求められます。この”機械図面通りに行う加工”というのは、作業者が第三角法により描かれた設計図面を読み解き、寸法・形状が合うように加工を行うというのが一般的です。最近では、NC化の流れに伴い、多くの製造業企業において図面を元に一度、CAD・CAMを作成した後に加工を行う事を行うことが一般的な流れとなっています。
当社では、汎用の旋盤、縦型フライス、横型フライス、ボール盤に加え、マシニングセンタを使用して機械加工を行っています。そのため、CAD・CAMデータが必要となるマシニングセンタを用いた加工を行うワークと汎用機を用いた機械加工を行うワークとを分類し、マシニングセンタによる加工を行う図面の場合にはプログラムの製作を行い、機械加工に当たっています。
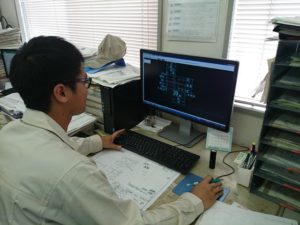
機械加工品 CADデータ化
③ ワークの形状製作
機械加工においてまず行うのは、ワークの形状製作です。一般的に機械加工で製作をするワークは、細かい寸法精度や穴加工等の追加工が指定されていますが、すべてを一度に加工するのではなく、大体の形状をつくる粗加工の工程がまずは入ります。この粗加工工程は、最終的なワーク形状が丸物形状であるか、角物形状であるかにより使用する加工機が異なってきます。そこで以下では、丸物形状、角物形状の加工について見ていきます。
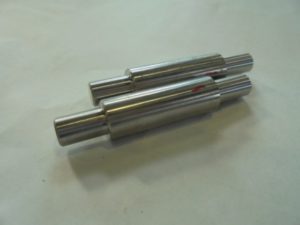
丸棒材
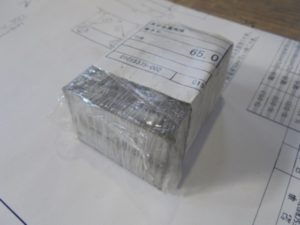
ブロック材
③-1 ワークが丸物形状の場合
ワークが丸物形状(軸物形状)である場合には、旋盤により粗加工を行います。下記に、当社で行った製作事例の写真を掲載しています。こちらのワークはサイズφ40×50mmの搬送ラインで使用する機械部品で、内径にキー溝加工が施してあり、端面にはc面取りを行っています。このような形状となるとまずは、丸棒材を調達し、片面ずつをチャッキングし、内径に対する止まり穴の加工と角部へのC面取り加工を行うことになります。ここまでが、下記の写真の場合における丸物形状品に対する粗加工工程となります。上部にある穴加工やキー溝などの加工は追加工工程となる為、③でご紹介をします。
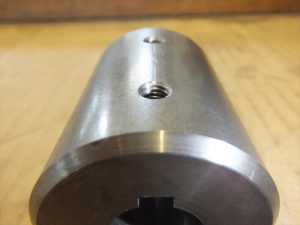
搬送ライン用 ステンレス部品
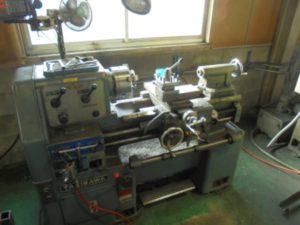
汎用旋盤
③-2 ワークが角物形状の場合
次に、ワークが角物形状である場合について見ていきます。角物形状の場合には、ワークサイズによりその加工方法は異なっており、当社の場合であれば、サイズのあるものは縦型フライスやマシニングセンタにより粗加工を行い、小さいワークの場合には、四つ爪チャックを使用した旋盤により加工を行います。
下記の写真は、サイズH45×W67×D420の搬送装置に使用される設備パーツ品で、こちらもブロック材から粗加工を行っています。具体的には、写真の角部にあるC面取りと最終的に高い平面度が求められる為に、面に対して粗加工を行っています。最終的には、ボール盤によるネジ穴加工と平面度だしの全面研磨加工を行っています。こちらの工程は、先ほどの丸物加工と同様で、追加工工程となる為、③で説明を行います。
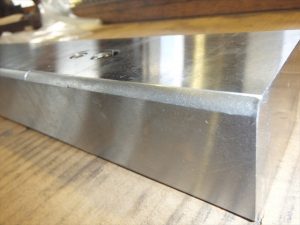
搬送装置用治具
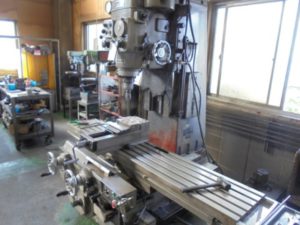
縦型フライス
④追加工工程
ここからは、粗加工後の追加工工程についてみていきます。追加工の代表的な例としては、穴加工や溝加工、キー溝加工、研磨加工等があります。ここでは『産業機械 一貫加工組立.com 』で加工対応が可能な追加工工程を大きく3つに分類し、各々の加工について製品事例をもとに説明をします。
④-1 穴加工・溝加工
機械加工による追加工の中でも、穴加工や溝加工といった加工は非常に一般的な追加工と言えます。特に、当社が得意とする組立工程が必要となる産業機械向けのユニット品の場合には組立を行う為に、追加工は必須のものと言えます。
下記の写真は、先ほどのブロック形状品の加工事例として紹介をした搬送装置用治具です。二つの部品と組み立てる構造となっている為に、ネジ穴加工を施しています。こちらの場合には、ボール盤を使用して穴加工を行いました。
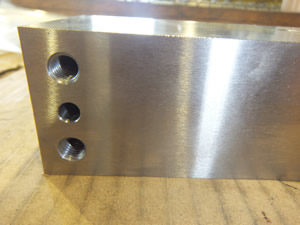
ボール盤によるネジ穴加工
また、当社では、マシニングセンタや縦型フライスも保有しているので、ボール盤だけでなく、これらの機械を用いて穴加工を行う場合もあります。
加工機の選択基準としては、直角度が必要となる穴加工の場合には縦型フライスをし、精度が不要となる場合にはボール盤を使用します。また、溝加工や穴加工等、複数の追加工が必要となる場合には、マシニングセンタを使用します。また、サイズのある製品の側面への深穴加工の指定がある場合には、横型フライスを用います。
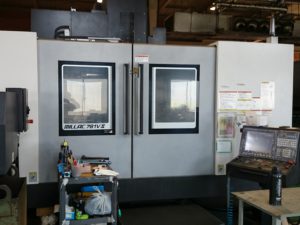
マシニングセンタ
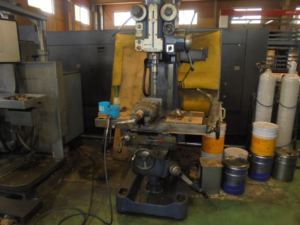
ボール盤
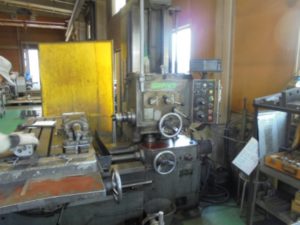
横型フライス
④-2 自由局面形状や端面の角部への精度だしなどの加工
次に、放電加工機を使用することで可能となる追加工事例について、ご紹介をいたします。放電加工機だからこそ可能となる加工とは、角穴形状や自由曲面形状などが該当し、これらはドリルの形状(小さいRが残ってしまう等)や加工機の主軸の動きの制限により、加工が不可能であるとされているものです。このような形状が必要になると、一般的には放電加工機を用いて加工が行われます。当社の場合にも放電加工機を一台保有し、ドリルによる機械加工では難しいとされる加工を行っています。
実際に行った加工事例としては、丸物形状の粗加工事例として紹介した、産業機械のライン部品がそれに当たり、キー溝加工部分を放電加工により仕上げています。キー溝加工は、角部が丸くなっていると組立後に嵌めあいが悪く、ユニット部分の不良の原因となりますので、ワイヤーカット放電加工機を用いれ角部がしっかり立っている形状の加工を施しています。このほかにも3次元曲面などの加工も放電加工を用いることで可能となります。
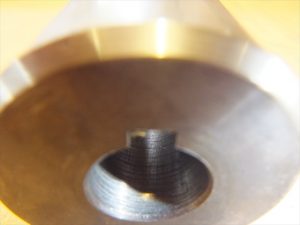
キー溝加工部
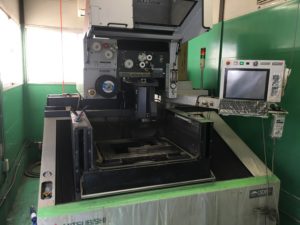
ワイヤー放電加工機
④-3 研磨加工仕上げ
産業機械等の部品・ユニット品製作を行う当社では、部品の仕上げ工程で塗装前に研磨仕上げを行う場合が多くあります。これは、産業機械部品の多くが摺動面や回転部で使用される為であり、図面上では平面度にして0.02~0.05と言った指定がなされている場合が多くあります。
実際に、産業機械 一貫加工組立.comで製作を行った事例として、下記のような機械部品があります。
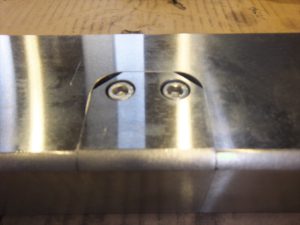
研磨加工仕上げ
こちらの機械部品は、搬送装置に使用される設備パーツで2部品を組み合わせています。先ほどまでの穴加工などを経て、ねじ締結を行っています。その後、上記の写真の面が摺動面となる為に平面度を保つ為に研磨仕上げを行いました。当社では、平面研削盤を一台保有しており、機械部品に対して必要となる平面度出しなどの研磨加工に対応が可能となっています。
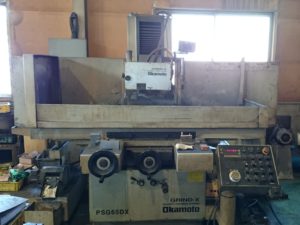
平面研磨加工機
⑤ 溶接工程
『産業機械 一貫加工組立.com』では、多くの機械部品をユニット品として引き受けしており、これまでに紹介してきたような機械加工はもちろん板金加工品を含めて、一貫生産を行い、溶接により部品を接合し、組み上げた後の御客様に提供している製品がほとんどとなります。その為、社内において溶接場を設け、8名体制で溶接組立に対応をしています。また、溶接を行うと材質にや形状によっては大きく歪が出てしまう場合があるので、歪み取りやグラインダ-による仕上げ工程も行っており、当社のラインの特徴は、溶接組立・仕上げ工程までを溶接工一人ひとりが対応し、完成まで一人で完結させる工程を組んでいる点にあります。下記は、実際に溶接組立中の写真となります。
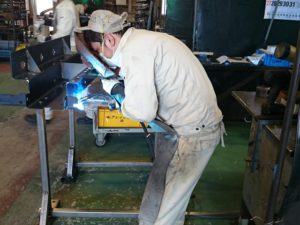
溶接組立
下記の写真は、産業機械用のブラケット品であり、機械加工に加え、当社で溶接組立にも対応をしています。
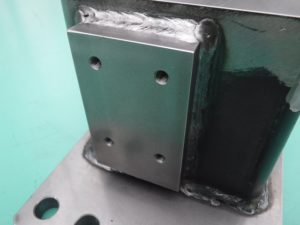
溶接組立品
⑥ 組立工程
次に、溶接組立以外の組立方法についてもご紹介をします。当社では、建築資材も多く取り扱っており、溶接ほど強度がいらず、組立を行いたいという部品を依頼される場合があります。そのような場合においては、ネジ締結という方法を用います。どのような方法かというと、ネジを使用して2個以上の部材を締結する方法です。締結の種類としては、ナット締結、小ネジ締結、セルフタップ締結などがあります。市販の締結部品の規格に合わせて設計をしていただければ、コスト面でも非常に優位性のある締結方法で、締結力を都度調整でき、克必要に応じて分解できることが溶接と比較した場合のメリットとして挙げられます。一方で、先に説明をしたように溶接組立と比較すると強度の面で劣る部分がありますが、専門技術を要する必要が無いため、リードタイムの削減が可能となります。
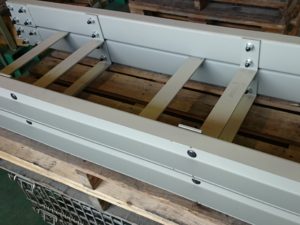
ねじ締結組立品
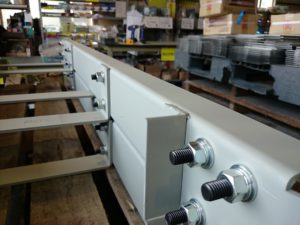
ねじ締結組立品①
⑦ 表面処理工程
『産業機械 一貫加工組立.com』が提供している機械組立品、溶接組立品の場合には、産業機械を始めとする摺動部品や回転部品であったり、外気にさらされる建築資材である場合が多くあり、めっき・塗装をはじめとする表面処理工程が必要となります。当社では、塗装工程を内製化しています。その結果、材料調達~機械加工組立・溶接組立~塗装までを一貫対応することが可能です。また、特殊なめっき処理等は近隣の協力工場へと委託することで、対応が可能となっています。

塗装工程
⑧ 検査・納品
『産業機械 一貫加工組立.com』が提供している機械組立品、溶接組立品の加工~組立、塗装までの一貫生産体制について、紹介をしてきました。最後にご紹介するのが当社が保有する品質保証体制についてです。先に、説明をしましたように材料の手配おける安全性の確保とトレーサビリティについてはミルシートを材料商社から取得することで、保証しています。
また、加工品に対しては、2001年に国際品質マネジメント規格であるISO9001を取得し、材料手配・調達から板金加工、機械加工、溶接、組み立て、塗装、出荷までを徹底した品質管理体制の下で行っています。
長谷金属の製作している板金組立品、機械加工組立品は、輸送機器や工作機械、産業機器など、高い精度と安全性が求められる業界に多く使われています。そのため、品質管理も高いレベルが求められており、納品時においても、キズが製品につかず、搬送が効率的にできるような梱包などにも対応しています。
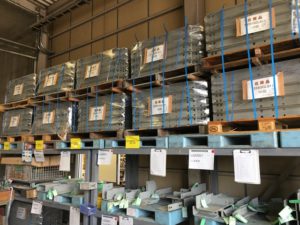
品質検査後、キズを防ぐための梱包にも対応
まとめ
如何でしたでしょうか?
上記工程はあくまでも一例ですが、機械加工は図面を基に、丸形状は旋盤、角形形状はフライス、複雑形状品はマシニングと、ワーク形状によって工作機械を選択します。また、ワークのロット数を踏まえて汎用機かNC機かの、選択も行います。量産品ではなく、多品種微量のワークの製作をしている等の条件も工作機械の選定要素となるのです。お客様へ最適なコストで提供しようとすればするほど、その選択する工程・機械は都度変わるのです。
そこに組立溶接が入ると、機械加工で仕上げた部品に対して、溶接技術者が金属部分を接合します。溶接組立といっても、TIG溶接や、CO2溶接、MAG溶接等の種類があり、ここでも、形状や材質に合わせた溶接機の選択が必要になります。また、加工機の選定ではありませんが、溶接によって発生したスパッダや溶接バリを除去するグラインダー作業を経て、溶接組立品が完成します。
『 機械加工 溶接組立 』と一言でいえばそれまでですが、機械加工をする為に必要な工作機械は、構内スペースに多少なり密集して配置する傾向にありますが、溶接作業場や溶接バリ取り作業場、組立作業場はスペースを確保する傾向にあります。この傾向から、機械加工を中心と金属加工業は空いたスペースには工作機械を配置する一般的であり、一人で何台ものNC工作機械を稼働させていることが多くなっています。一方で、溶接組立場は、工場内の敷地面積を比較的とれる加工業が得意としています。溶接ロボットがあったとしても、溶接機1台を稼働させるためには、1人の職人が配置され、また溶接技術者の溶接レベルがそのまま、溶接組立品の品質に直結していきます。
ほかにも塗装や表面処理・めっき加工等の仕上げ工程も必要に応じて求められこともあり、機械加工と溶接組立、仕上げ加工まで、1社にて対応できれば製作コストと管理工数も削減できることになります。
長谷金属の「機械加工+溶接」の動画はコチラ
当サイトでは、このような内容を技術ハンドブックに掲載しております。ぜひ、ご活用下さい。また、お気軽にお見積り、技術相談も受け付けております。